Services
Hot Insulation ( Rock Wool )
Preparations
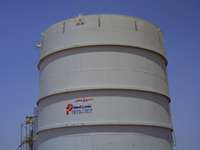
-Construct Steel Scaffolding Around the Equipments
(Tanks, boilers, Heat exchanger, Skid, ….. ) to be insulated.
– surface to be insulated shall be Cleaned free of oil, grease and all other foreign matter and shall be free from moisture prior to the application of any insulation if any.

–Preparation of equipments ,as Welding of Fastener Flat barIron Spacer Ring and Fastener pins around the equipments to be insulated
– Spacer steel ring should be insulated using insulation tape to prevent Heat transfer to Aluminum metal jacket During the flat Bar Iron
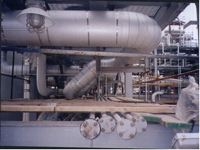
Insulation of Valves & Double flanges
– Fabrication of Removable boxes for the Valves and flanges to be carrying out during maintenance works according to specification.
– Any penetration of the metal jacket by pipe supports, nipples etc., will be weatherproofed by metal flashing.
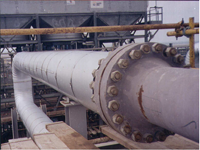
Insulation Material
Installation of insulation material ( mineral Wool ) on the equipments to be insulated Product data sheet available
– Securements for basic insulation will be 0.5 * 19 mm Or 1mm galvanized wire to Fix the insulation material (Rock wool) on the surface to be insulated.
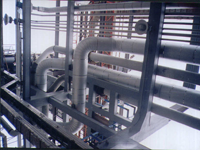
Accessories &auxiliaries Materials
– Fix the metal jacket using Galvanized, S.S tapping Screw Type(0.5*10)
– The proper number 7 Screw / M. long
– Using a sealant material (silicon Or mastic tap)
– Site Clean-up and removal of All Materials , Lost Materials And Equipments After Finishing the insulation job.
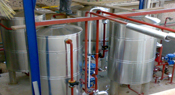
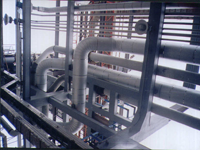
Metal Jacket
– Fabrication of metal jacket ( Aluminum , Galvanized Steel , Stainlesssteel )according to specification.
– Making a longitudinal and circumference seam to metal jacket, which shall be appliedto ensure a tight fit over the insulation and to prevent any lifting of the lapping edge at the longitudinal seam. All longitudinal seams shall be staggered on alternative side of the pipe and laps shall be located togive maximum protection from wind and rain.metal jacket sheets shall be overlapped male to female in order to increase the regidity.
The metal shall be cut sufficient length to provide a minimum 50mm lap at the longitudinal seam.
The jacket shall be applied with a minimum circumferential lap of 50mm.
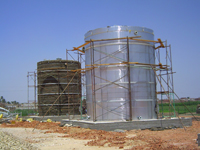
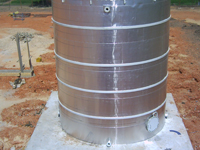
Insulation of Pipe fitting
– The insulation for pipe elbows shall be fabricated from mitred segmentof the straight pipe sectional insulation, cut to conform to the radius of the Elbow.
– The proper number of mitres is required on an Elbow so as
provide a goodclosure. A general guide is as follow: to 4″pipe is 4 mitres, to 6″ pipe is6 mitres, to 10″ pipe is 8 mitres , to 18″pipe is 10 mitres , and above is 12 mitres.
– Any penetration of the metal jacket by pipe supports, nipples etc., will beweatherproofed by metalflashing
Cold Insulation
– Fabrication of metal jacket according to specification.
– Making a longitudinal and circumference seam to Aluminum metal jacket, which shall be applied to ensure a tight fit over the insulation and to prevent any lifting of the lapping edge at the longitudinal seam. All longitudinal seams shall be staggered on alternative side of the pipe and laps shall be located to give maximum protection from wind and rain.
– metal jacket (Aluminum , St.St. ) sheets shall be overlapped male to female in order to increase the rigidity.
– Making Pre. Foam spacer ( insulation thickness ) between the metal jacket and the body to be insulated using preformed foam.
– Installation of (Aluminum , St.St.) on the pipelines and equipmrnts to be insulated.
– The metal shall be cut sufficient length to provide a minimum 50mm lap at the longitudinal seam.
– The jacket shall be applied with a minimum circumferential lap of 50mm.
– The insulation for pipe elbows shall be fabricated from mitred segment of the straight pipe sectional insulation, cut to conform to the radius of the Elbow. The proper number of mitres is required on an Elbow so as provide a good closure. A general guide is as follow: to 4″pipe is 4 mitres, to 6″ pipe is 6 mitres, to 10″ pipe is 8 mitres , to 18″pipe is 10 mitres , and above is 12 mitres.
– Any penetration of the metal jacket by pipe supports, nipples etc., will be weatherproofed by metal flashing.
– Fabrication of Reducers and Tees according to specification.
– Fix the metal jacket using stainless steel bands.
– Using a sealant material (silicon Or mastic tap) to close the holes.
– Install the Raw materials polyurethane (polyol /isocyaiate)into injection machine tanks.
– Polyol is designed for the production of polyurethane using for Cold insulation. Reaction of Polyol with isocyanate give foams with excellent flow ability, resulting in a Very even density distribution. Good physical properties and dimensional Stability are provided as well as good adhesion to usual facings and short Demold times.
– Cleaning the pipelines and equipmrnts after injection process.
Acoustic Sound Insulation